Etching
with
Air
Regenerated Acid Cupric Chloride
By
Adam Seychell
(Last modified 5 November 2005)
(mirrored on timhollars.com with all rights to Mr. Seychell)
This page describes
some practical information on
how to use air regenerated acid cupric chloride to etch printed circuit
boards at home.
Contents
Introduction
The information in this guide is based on my discoveries using
and
exploring cupric chloride etchants at home. While investigating air
regenerated cupric chloride as circuit board etchant, I felt there was
general lack of detailed information available, especially in hobbyists
circumstances. Having since learned much more about this etchant
including practical methods, I was inspired to write this guide to
share what
I have learned, and hopefully help other hobbyists who
want to understand more about using cupric chloride at home.
Why Acid Cupric Chloride
Of the
several types of etchant
chemistries the hobbyist
can
choose, acid cupric chloride (also called acid
copper(II)
chloride or just cupric
chloride) is one of the more interesting types, since it
has the ability to be regenerated, or replenished, without having to
throw away the solution. This is the reason why cupric chloride is one
of two main
etchants widely used by PCB fabricators. The primary advantages of
cupric chloride in a hobbyist prospective is that a maintained solution
never becomes exhausted. The disadvantage is the extra work is required
for occasional bath maintenance. People who sparingly etch circuit
boards, will
only
want a temporary and low complexity etch method. For simplicity,
you cannot get any easier than pouring some ferric chloride or ammonium
persulfate in a
plastic container, heat it a little in the microwave oven, and immerse
the PCB. More serious people may go to the effort of
setting
up a vertical bubble etching tank. It is these people who
may find it beneficial to own an etch tank that
does not deplete or decline in etching speed.
Figure 1
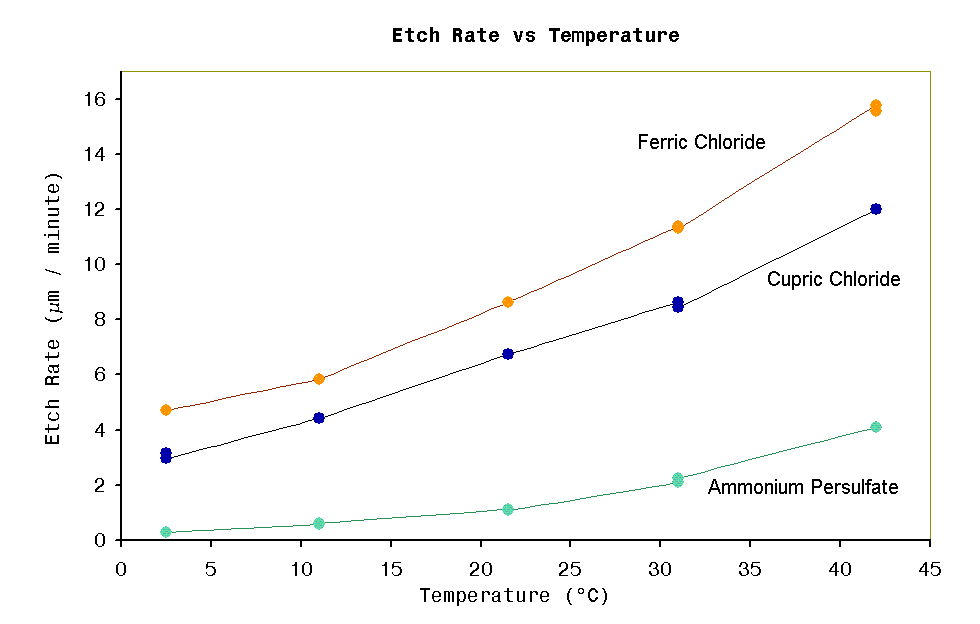
Figure 1 shows graph of relative etch rates vs
temperature for three
different etchant chemistries, all solutions were freshly prepared. Ferric
chloride:
specific gravity =1.47. Cupric chloride: HCl
concentration=2.7M, specific gravity=1.27, cuprous ion < 2g/L. Ammonium
persulfate: concentration=200g/L. Etch rates were determined
with my copper etch rate
apparatus and vigorous air bubbling was used for solution
agitation. The aim of these measurements were to find if unheated
solutions give acceptable etch rates. The ammonium persulfate is
obviously not suitable for room temperature operation. However the
ferric chloride and cupric chloride still may be useful down to zero
degrees. Temperatures > 42°C were not tested since both ferric
chloride and cupric chloride would create too much fuming for a
practical hobby etch tank.
Added note: The persulfate test showed considerably reduced etch
rate compared to ferric chloride or cupric chloride. According to
experience with conventional bubble etching, the 50°C persulfate
solutions are only marginally slower than ferric chloride. A
possible theory why my tests showed only 1/4 etch rate of ferric
chloride at 42°C, is that vigorous solution agitation has a greater
accelerated effect on ferric chloride or cupric chlorides than it does
on persulfates. This agitation acceleration could explained by the
insoluble copper(I) film formed with ferric chloride or cupric
chloride as being the limiting factor on etch rate. Persulfate on the
other hand do not form insoluble surface films, and so etch rate is
limited only by solution kinetics. When agitation is strong then
the film is removed quicker allowing a rapid increase in etch rate of
ferric chloride or cupric
chloride solutions, while in persulfates, etching it still limited by
rate of fresh persulfate ions encounter the copper surface.
Chemistry
Copper metal is
oxidized by one
cupric ion to produce
two cuprous ions,
[1] Cu0 + Cu2+
→
2Cu1+
The Cu1+ ion is not soluble in water but it can be made
soluble with the help of coordination ions which are ions that
surround the Cu1+ atom by electrostatic attraction.
The chloride ion, Cl -,
is one such coordination ion for Cu1+. If one
prepares a solution containing Cu2+ and Cl - ,
for
example by dissolving cupric chloride in water, then that solution
should have the ability to etch copper metal because the Cu1+
ions are soluble in such a solution, and reaction [1] can proceed. In
reality, the Cu1+
ions need a relatively large concentration of Cl - in order
for them to be soluble in water.
The overall equation during etching is;
[2]
CuCl2 {aq} + Cu {s} → 2CuCl {aq}
Regeneration
The cupric chloride etchant can be restored or 'regenerated' to its
original state by oxidizing the Cu1+
ions back to Cu2+ by an addition of an oxidizing agent.
Common oxidizing agents used in industry are hydrogen peroxide,
sodium
chlorate,
dissolved chlorine and dissolved oxygen. In this
discussion we
will only concerned ourselves with oxygen regeneration by dissolved
air.
The disadvantage of air regeneration compared to chemical regeneration
is its slow speed due to difficulty of dissolving sufficient quantities
of air into solution. But air regeneration does have the advantages of
being freely available and impossible to add in excess. The equation
for regeneration by
oxygen is;
[3]
2H+ + Cu1+ + O{aq} → Cu2+
+ H2O
You can see H+ is consumed in the above reaction, and
so what better way we can provide hydrogen ions other than from
hydrochloric acid. With excess hydrochloric acid in the mix, the
chloride balance is always maintained, and the solution effectively
just
grows
as it consumes four ingredients during its lifetime. These include;
copper
metal, oxygen (from air), hydrochloric acid, and water.
The overall equation during regeneration can be written as;
[4]
2HCl {aq} + 2CuCl {aq} + O {aq}
→ 2CuCl2 {aq} + H2O{aq}
In practice, the concentrations of Cu2+, Cu1+,
and free acid, affect the etching speed. In particular the Cu1+
ion has a large affect on etch rate. Cu1+ has much lower
solubility compared to Cu2+ and because it is
generated directly at the surface of the copper, where the reaction is
taking place, its presents will inhibit etching. The Cu1+
ions therefore must be removed away quickly as possible from the
copper surface
in order to maximize etch speed. One way of achieving this is to
maximize the solubility of Cu1+so it can quickly diffuse
into the bulk solution. Diffusion of Cu1+ from the copper
surface is increased by keeping concentrations
in
the bulk solution to a minimum.
Operating
Parameters
Operating air
regenerated cupric
chloride etchant requires more attention to
operating parameters than it would to commonly used
hobby etchants, for example, ferric chloride or ammonium persulfate.
Etch speed will be impaired if bath parameters operate too far out of
range. When etching is too slow then the benefits of using cupric
chloride may be lost. As the main objective of this guide is to
demonstrate how to properly use
air regenerated cupric chloride, I present here the results from
a
series
experiments
I had done which demonstrate the effects of etch rate under various
operating conditions. It turns out the major variables affecting
etch rate are
temperature, Cu1+ concentration, and free
acid concentration. For
a detail description of the experimental method, see my copper
etch
rate
apparatus. Below is a
discussion of my results and a summary giving recommended operating
parameters.
Figure 2
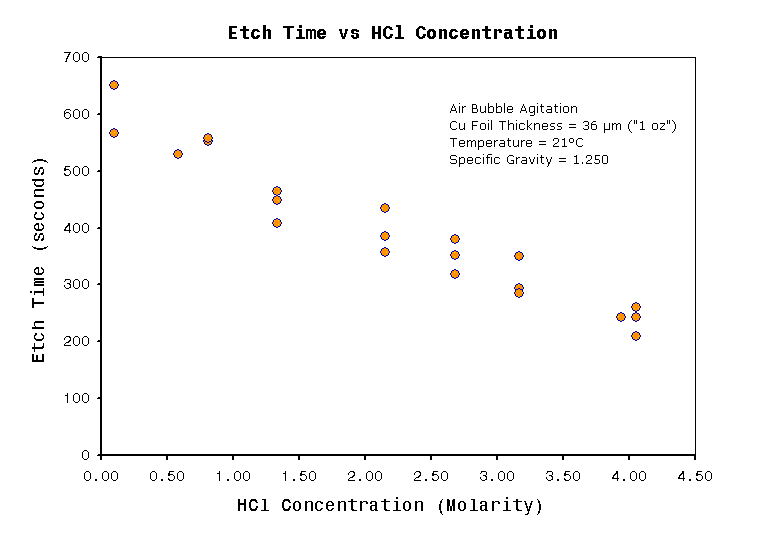
Figure 2 Shows that etch rate
is strongly affected by acid concentration. The relationship is fairly
proportional, and the plot shows no etch time minima. The problem
operating
at very high acid concentrations is excessive fuming from open
tank bubbling etching solutions. Therefore the maximum limit to acid
concentration depends on the level of fuming tolerated. Higher
temperatures also contribute to HCl fumes. As a rough guide I would not
recommend HCl above 4M in enclosed spaces at temperatures
above 25°C. The smell and corrosive nature of HCl from such
solutions
may cause other problems. I found that at acid concentrations of about
2.5~3M, and at temperature 30°C are about my preferred limit for an
open top air bubbling tank. Concentrations under 1M are very low
fuming,
but etch speed will be compromised. The graph of figure 1 may help you
choose
acid concentration based on relative etching time.
Figure 3
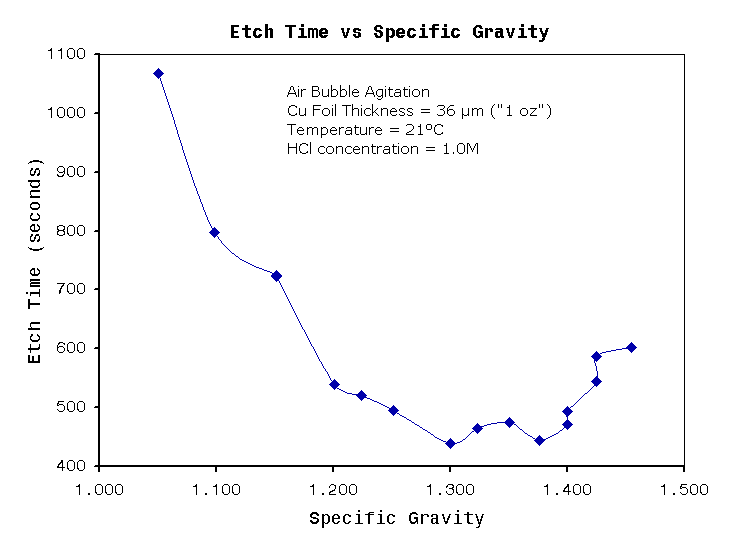
Figure 3 shows that etching
time is only effected when specific gravity becomes extremely high or
extremely low. The specific gravity is mostly dependent on copper
concentration , and partly dependent on acid concentration. The flat
plateau in the graph occurs when specific gravity in the range of about
1.200
to 1.400. This corresponds to a vary large variation in copper
concentrations (sorry I don't have numbers). I would not recommend
operating at 1.200 or at 1.400, as these values are getting too close
to the plateau ends. According to a cupric chloride
technical
document from Chemcut corporation , they recommend optimum
specific gravity to be between
1.240 to 1.330. This range lies about directly in the middle of figure
2. For the hobbyist a safe range for specific gravity may be between
1.22 and
1.38. This may sound like a small numerical difference, but the
physical
change in copper concentration is quite large.
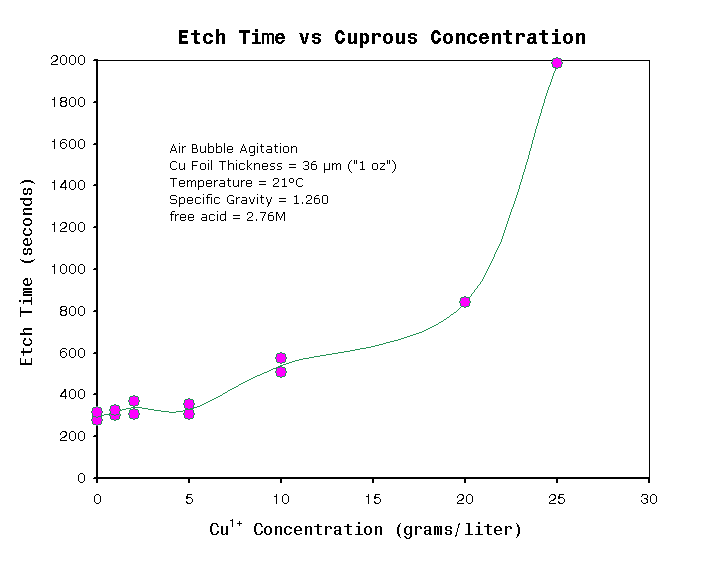
Figure 4 shows etch rates, where each solution contains a
different initial concentration of Cu1+.
It
is well known that
etch rate of cupric chloride are strongly affected by relatively small
concentrations of Cu1+, see CuCl chemistry.
It is therefore expected that etch rate will decrease as more copper is
dissolved when in a limited volume of solution. The graph demonstrates
that when more than approximately 5 g/l of copper is dissolved in
solution and is not
regenerated (i.e the formed Cu1+ is not
oxidize to Cu2+) then the etch rate begins to decrease, and
becomes almost zero when monovalent copper reaches above 20g/l, which
is almost at saturation. It
also predicts the minimum volume of solution necessary to dissolve a
given mass of copper without sacrificing etch speed. For typical double
sided PCB with 36μm thick foil thickness and 50% pattern coverage, then
a safe estimate of minimum volume of etchant per unit board area
calculates out to
be 1.6 liters/dm2 (16 ml/cm2). However air
is
normally bubbled through the solution during etching, and so the
solution will be in the process of regenerating during this time.
Because of this, minimum volume will be actually be less than predicted
and depends
directly on the
efficiency of the air regeneration system. In other words, this 1.6
liters/dm2 value should be treated as being
very conservative.
Summary
Table 1. Recommended bath
operating parameters.
Parameter
|
Min
|
Max
|
Remarks
|
Free acid
concentration (molarity)
|
1.0
|
3.5
|
HCl fuming
increases
Etch speed increases. (see note 1) |
Specific
gravity (g/cm3)
|
1.220
|
1.380
|
Relatively
stable etch rate across range
|
Temperature
(°C)
|
0
|
40
|
HCl fuming
increases.
Etch speed increases. (see note 1)
|
Minimum bulk tank volume per
board area
(liters/cm2 )
|
0.016
|
-
|
Assuming 50%
track coverage, double
sided, 36 μm ("1oz") copper PCB.
|
Maximum monovalent copper ion, Cu1+
(g/liter) |
-
|
5
|
Color of
drops on white surface should appear
bright green to olive dark green. Any signs of
brown color indicates too high Cu1+.
Also see Figure 5
|
Notes
- The temperature and acid molarity both contribute to HCl
fuming. When temperature is at the high end of the range then acid
molarity should be reduced, and when temperature is low end then acid
molarity can be increased. These two parameters are best determined
through personal experience in your environment.
Bath Analysis
To keep bath
concentrations within in the range given in Table 1
it is necessary
to have some way of measuring what the concentrations are, and if
necessary, make appropriate adjustments, see Bath
Control . Fortunately the
range of these parameters is relatively broad, and so measurement
accuracy
and bath chemical adjustments will be very forgiving. The three
important parameters to measure are;
- Acid concentration
- Specific gravity
- Cu1+(cuprous) concentration
Measuring Specific Gravity
The high copper content in cupric chloride etchants give them a high
density. Specific
gravity measurement then becomes a reliable (and simple) method of
estimating copper. The easiest way to measure density is with a glass
hydrometer.
If you use a vertical etching tank that is > 200mm deep
then a typically glass hydrometer could be immersed directly
in the tank. The other way is to use automotive lead acid battery
hydrometer, although the highest reading of these devices is usually
1.300.
Measuring Acid
Acid
concentration is measured by quantitive chemical analysis. This
analysis is best done by acid/base titration using
a strong
alkaline like sodium hydroxide as a titrant. According to Table 1
the wide tolerance of acid concentrations allows the simplest
titration method conceivable.
Normally, titration of hydrochloric acid (a strong acid) is performed
with an acid-base indicator, but this solution contains very high
copper levels which interferes with color, and pH, making it
necessary to carefully choose the correct pH indicator. Alternatively,
you can take advantage of the
dissolved copper and use it as an indicator. The end point is indicated
by looking for the first signs of copper hydroxide precipitation,
since at this point all the acid has reacted and is just beginning to
react with the cupric chloride. If you do not own
titration equipment, and don't want to fuss around buying equipment,
then I
recommend the following technique;
List of items needed (see a photograph)
- dry sodium hydroxide, NaOH (> 95%)
- 500ml ~ 1liter plastic bottle (any type)
- 1 ml graduated syringe
- 30~100ml clear glass bottle or jar
First step is to prepare
the titrant, which will be a
1.0 Molar sodium hydroxide solution. This solution can be made by
dissolving 40 ±4 grams of sodium hydroxide per liter of
water (any water thats drinkable will be pure enough). The sodium
hydroxide I've seen at supermarkets is normally %99 and comes as tiny
grains that should be free flowing. If you don't have access to a set
of
scales with 1 gram resolution then it is possible to obtain a known
mass
by measuring volume of the dried sodium hydroxide grains. I measured
density of these grains to be about 1.13 g/cm3. For example,
you can use a 20
ml kitchen measuring spoon to get ~22.6 grams of NaOH and
dissolve this in 550 ml of water using a kitchen measuring jug to get
approximately 1.0 Molar solution. Another possibility to obtain 40g of
NaOH is to take a sample to your local post office and ask them to
weigh it for you. Store the titrant in a
clearly labeled plastic bottle. Preparing this is a once
off procedure.
Performing the Titration
Fill the glass bottle with
approximately 10 ~ 30 ml of warm water. Using the graduated
syringe, add 1.0 ml of the etchant solution which is to be tested (the analyte).
To
avoid corrosion
of the stainless steel
needle flush
the syringe immediately with the diluted solution in the bottle.
Now, take up 1.0 ml of
sodium hydroxide titrant into the syringe, and then immerse the needle
in to
the solution. Slowly add the titrant by pressing the plunger down while
at
the same time move the syringe around in circles to keep the solution
stirred. You should see localized copper
hydroxide
formed next to where the sodium hydroxide contacts the diluted etchant
solution. Before the end point has been reached, the copper hydroxide
formed will redissolve in the unreacted acid
upon stirring. The end
point
is indicated when solution first begins to loose clarity throughout.
See the titration
photographs to get a better
idea of what I'm talking about. Hold
the solution up to a bright light or torch to help observe the
turbidity. While approaching towards the end point the copper
hydroxide increasingly takes longer to re-dissolve in the unreacted
acid
because
there is less free acid available. Higher temperatures will speed up
the
reaction and is why hot water was suggested to initially to fill the
bottle. Once the end
point has been reached then
make note of the total volume in cm3 of
titrant that was added. This number will equal the
free acid molarity (moles per liter) of the etchant.
Testing for Cu1+ ion
The appearance of the solution is probably the
best way of determining
if Cu1+ concentrations is too high. Figure 5
shows
color comparisons at various concentrations of dissolved Cu1+
ions. You can clearly see that Cu1+ in
solution makes it extremely dark, and even small concentration in the 1
g/Liter range will
make the solutions darker and more diffuse than normal. When
Cu1+ is completely
removed or exists only in trace amounts then the etching solution is a
deep green transparent color due to Cu2+. The
concentration of Cu2+
is normally so high that you cannot see through more than about 10
mm of solution depth under normal light. Therefore to check if Cu1+
concentration is acceptable, you can look at drops of solution
sitting on a white surface.
On a side note, when the etchant solution is
sufficiently diluted then Cu1+ precipitates out as cuprous
chloride (a white solid). Visible signs of the white precipitate
however only
show up when concentrations are very high, or too high for reasonable
etching performance.
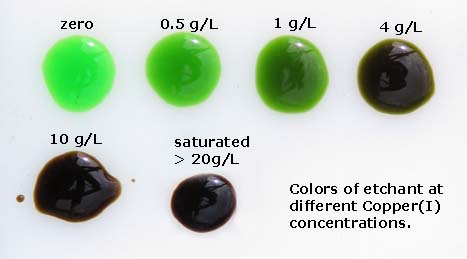
Figure 5. Photo of
different etchant solutions on a white surface. Each color shows
different concentrations of
dissolved Cu1+ ions.
Bath Control
Three bath parameters need
controlling: Acid concentration, specific gravity and Cu1+concentration.
I recommend bath adjustments be made in that order because some
adjustments made to one parameter will also affect another. Its always
a good practice to remeasure the bath after you've made modifications.
Acid Control
If acid is too high, and the specific
gravity is already low, then water should not be added to the etchant
in attempt to reduce acid concentration. The specific gravity may drop
too low. In this case there no way of reducing acid except by
allowing the HCl gases to evaporate or get consumed during normal
etching. In
other words don't worry about high acids.
To increase acid concentration then
concentrated hydrochloric acid can be added directly to the tank. The
volume of concentrated hydrochloric acid to add can be estimated with;
[7] volume of concentrated hydrochloric acid (liters) = VT
× (CF - CI) / ( Cacid
-
CF )
where
VT = initial etchant volume (liters)
CI = the initial etchant acid molarity
CF = the final etchant
acid molarity
Cacid = the molarity of concentrated
hydrochloric acid being added, see Table 2
Specific Gravity Control
To increase specific gravity the solution must
be evaporated.
To decrease specific gravity water must be added.
Cu+1 Control
To decrease Cu1+ concentration the bath
must be aerated. See chemical equation [4].
If you want to be pedantic then the solution can be
aerated after each etching job until the color is a completely
transparent bright green, i.e. Cu1+ concentration << 1 g/L.
See figure 5
Tank
Considerations
<not finished>
Preparing
Cupric
Chloride Etchant
There is
multiple
ways one can prepare
a solution of cupric chloride and hydrochloric acid. The table below is
list of the two different methods which are described in in detail
below. All the preparation procedures described here will require
an empty fully functioning etching tank fitted with an air
bubbler. The solutions will actually be prepared in the etch tank.
Method
|
Chemical
Ingredients |
pros
|
cons
|
Metal + Air
|
Concentrated HCl
Copper Metal
Hydrogen Peroxide 3% (optional) |
Low cost
Ingredients widely available |
Long time to prepare (3 to 10
days)
|
Copper(II) Oxides
|
Concentrated HCl
Copper Hydroxide or Copper(II) Oxide
|
Quickest.
Least amount of labor
|
May prove difficult or costly
obtaining copper salts
|
Preparation using Metal + Air
If you are
hard up for cash, you can make copper chloride etchant from just scrap
copper metal and hydrochloric acid. This method prepares etchant by
dissolving copper in a solution containing a high concentration of acid
and a small concentration of oxidizing agent. The reason for the
oxidizing agent is that copper metal will not otherwise react with
hydrochloric acid. Two usable oxidizing agents are hydrogen peroxide
and Cu2+ ions (as cupric chloride). When Cu2+is
the used as the oxidizing agent then it brings up an interesting
situation. Provided free acid and oxygen are supplied then the reaction
of copper will be self perpetuating since the reaction product, Cu2+,
is also the reagent (the oxidizing agent). To solve the dilemma of
using Cu2+ as the oxidizing agent we have to somehow
initially added some to the solution for the reaction to start. It is
possible to create a small amount of Cu2+from copper metal
without needing any Cu2+.
When copper is wetted with hydrochloric acid and exposed to
air and fumes over a long period of time, it corrodes to form a mixture
of hydroxides and
chlorides coating the exposed surface. See
picture of copper oxides. This
reaction with air is slow,
and the
process can add several days just to get enough oxides of
copper to start the reaction. Once some copper is dissolved (oxidized),
the
reaction accelerates as more cupric ions build in the solution.
Alternatively you can use hydrogen peroxide and avoid having to have
any Cu2+to initiate the reaction.
The overall length of time it takes to prepare
etchant using his method
makes it a good time to do when you are busy doing other
thing in your life. Fortunately your attendance is only required once a
day or less. The
procedure outlined below should make a solution having specific
gravity of approximately 1.24
to1.26
and
a free acid concentration approximately 2.5M..
Note:
VT = final volume of
etchant solution in liters.
- Begin by weighing out 120*VT grams of copper
metal
and place into the tank. To
help speed up
the process, the copper metal should be finely divided so that
surface area/mass ratio is maximized. An ideal source of copper is that
of scrap multi stranded electrical power cables. I found that 1 mm
diameter stranded copper
wire
formed into a loosely bundled mass worked well. Ultimately the limit of
reactivity becomes how fast oxygen can be dissolved in solution.
- Without Hydrogen Peroxide
- Add 0.10×VT liters of
concentrated
hydrochloric acid ( > 25% weight) to the tank. There
should
only enough hydrochloric acid so that about 1/8 ~ 1/2 of the of the
copper is
immersed. That way the fumes
from the acid will react with air exposed parts of the copper and form
crusts
of copper oxides. I'd found best results when using concentrated acid,
even though most the HCl gas probably escapes in the air, it the
fastest
approach to get things started.
- Leave to stand for about 3 days or more (no limit) with the
tank top open to
allow oxygen from the air + HCl fumes to react
with
the copper. After this period the solution should be a dark brown
opaque
color. If the solution does not have this characteristic then it needs
further time. The parts of copper immersed in the acid may have visible
signs of etching while most of the copper above the acid level should
be coated in a crust of blue/green copper oxides. See picture of corroded copper metal in a tank.
- Add 0.60×VT liters of concentrated
hydrochloric acid and 0.30×VT liters
of water.
- With Hydrogen Peroxide
- Turn on the air bubbler, and
leave it going until the solution becomes transparent deep green
indicating the complete oxidation of all copper atoms into Cu2+.
The copper metal will slowly dissolve as air oxidizes the Cu1+
according to reaction [3]. The
process can take anywhere from one day to over a week depending on how
efficient the aeration is setup. An efficient aeration system will
cause the solution to rise 5~10°C due to the exothermic reactions
taking place. Acid will
continuously
be consumed by the reaction and so it can be a good idea keep it in
check. Provided acid is above 0.5M then the oxidation reaction should
not
be restricted. If acid drops to zero then the reaction will completely
stop. There will be a point towards the end where all the copper metal
has
dissolved, while the solution still containing large amounts of Cu1+,
as evident by the opaque dark brown color.
- Finally measure the free acid, and if needed add
appropriate amount of acid.
- Add water to bring at final
solution volume,VT, if needed..
Preparation using Copper(II) Oxides
It is very quick to make a etching solution from
salts of copper (copper(II) oxide or copper hydroxide) provided you
have these salts at hand. This method involves measuring out the
calculated
quantities of dried salt, concentrated hydrochloric acid and mixing
them all in the etching tank. For measurements, the use of kitchen
weight scales, and kitchen plastic measuring items are sufficiently
accurate (+-10%). The quantities of concentrated hydrochloride acid,
copper salt (copper hydroxide or copper(II) oxide) are determined by
the following equations which are based on a recommended dissolved
copper content of 120 g/L .
Concentrated hydrochloric acid = 3.78 × VT / Cacid
+ [H+] × VT
/ Cacid (Liters)
copper hydroxide, Cu(OH)2 =
184×VT (grams)
or
copper(II) oxide,
CuO
= 150×VT (grams)
Make to final volume with water.
Where:
VT = etchant final volume (liters)
[H+] = etchant final free acid
concentration
(moles/liter or molarity)
Cacid = molarity of the concentrated
hydrochloric acid used, see Table 2
Always perform acid analysis
after solution make up to confirm correct acid concentration.
Table 2, Relationship between
molarity and % weight of hydrochloric acid.
molarity
|
% weight
|
grams/liter
|
7.57
|
24.63
|
275.9
|
8.24
|
26.6
|
300.6
|
8.93
|
28.56
|
325.6
|
9.63
|
30.54
|
351.2
|
10.4
|
32.54
|
377.5
|
11.1
|
34.5
|
404.0
|
11.8
|
36.58
|
431.6
|
Disposal
In Australia
the EPA
regulates maximum copper in sewage discharge to 5 ppm. If you
have
etchant containing 150g/L of copper, that means a dilution 1:28000 is
necessary to meet regulations. This not a practical. If you have a
"lot" of solution to dispose of (and I'll let you define how much is a
"lot") then dumping would not be fair on the sewage treatment
facilities or our environment. There many ways of converting copper
solutions into a solid (or insoluble) form that you can dump and
hopefully not leach back into ground waters.
In alkaline environment copper ions precipitates out
of solution as copper hydroxide (or sometimes as black copper(II) oxide
under very strong or hot alkaline conditions). The standard method of
precipitating many dissolved metals in industrial waste waters, is to
put the waste liquid in a large vessel, and neutralize to pH above 9,
by
addition of sodium hydroxide, sodium carbonate, or lime. The solution
is left to stand for 24 hours or until all the hydroxides settle. The
problem with copper hydroxide is it does not compact very well in
solution and separation of solids only works well with small copper
concentrations < 1 g/L For a description of hydroxide precipitation
see Treating
Plating
Wastewater article on the pfonline website.
The sludge
method
I found this to be the only practical method of
precipitating cupric chloride etchants for disposal. This method
involves adding lime (calcium hydroxide) directly to the cupric
chloride etching solution. The copper is converted to hydroxide, just
as it would be if sodium hydroxide was added, however the reaction with
calcium is much less violent, and the sludge formed is a lot less
liquid. When the lime is initially added the acid will first
neutralize,
followed by the formation of copper hydroxide sludge. As more lime is
being added the color of the sludge will start out green
because
cupric chloride has been made insoluble (not enough water), and
eventually becoming a
consistent blue color once all copper is takes the form of copper
hydroxide. At this point you can either make cement out of it or dry it
and put it
to land fill in a sealed container.
Where to Buy
HYDROCHLORIC ACID, is one of
the most widely available strong mineral
acid around. It is often used as brick cleaner to dissolve cement, or
as a pH adjuster for home pools. Many hardware stores and building
supplies will sell hydrochloric
acid. HCl is usually sold in concentrated form. I've seen it sold
anywhere from 26% to 33% by weight, and the labeled
concentrations were shown to be surprising accurate.
SODIUM HYDROXIDE is available in pure form most supermarkets < 1kg.
Common synonyms are caustic soda, soda lye, lye. I've tested various
brands and were shown to be > 99.0%, given the limitation of my
measurement accuracy. The powder should be dry and free flowing. NaOH
is very hygroscopic so minimize time with lid off.
COPPER metal is best obtained from scrap metal recyclers. Copper is one
of the easiest metals to recycle and all the scrap metal recyclers I've
ever visited had piles of scrap electrical power cables.
COPPER(II) OXIDE, is often used as a black pigment for paint
manufacture. I have never shopped around for copper(II) oxide, so I
don't know if there exists a cheap source of a few kilograms. I'd
imagine expensive sources would be laboratory supplys, and art
supplys who sell pottery glazing pigments.
COPPER HYDROXIDE, is available at some gardening stores sold as a
fungicide. If you plan to make 10+ liters of etchant, it may be an
expensive source of copper salts.
LIME, available from gardening stores, and from building suppliers.
HYDROMETER, laboratory supplies would be my first choice for a
hydrometer.Some home brew wine suppliers sell hydrometers too. An ideal
range would be 1.200 to 1.400. Hydrometers are priced according to
accuracy, so anything with specific gravity accuracy of ±0.025
or
better will be
ok. A hydrometer used for measuring automotive lead acid batteries will
be suitable for cupric chloride etchants, except maximum reading will
usually be limited to 1.300.
1.0ml GRADUATED SYRINGE, are available from just about any pharmacy.
The 1 ml disposable syringes are often used for delivering insulin.
Copyright© 2005 Adam Seychell. All rights reserved.
See
Copyright